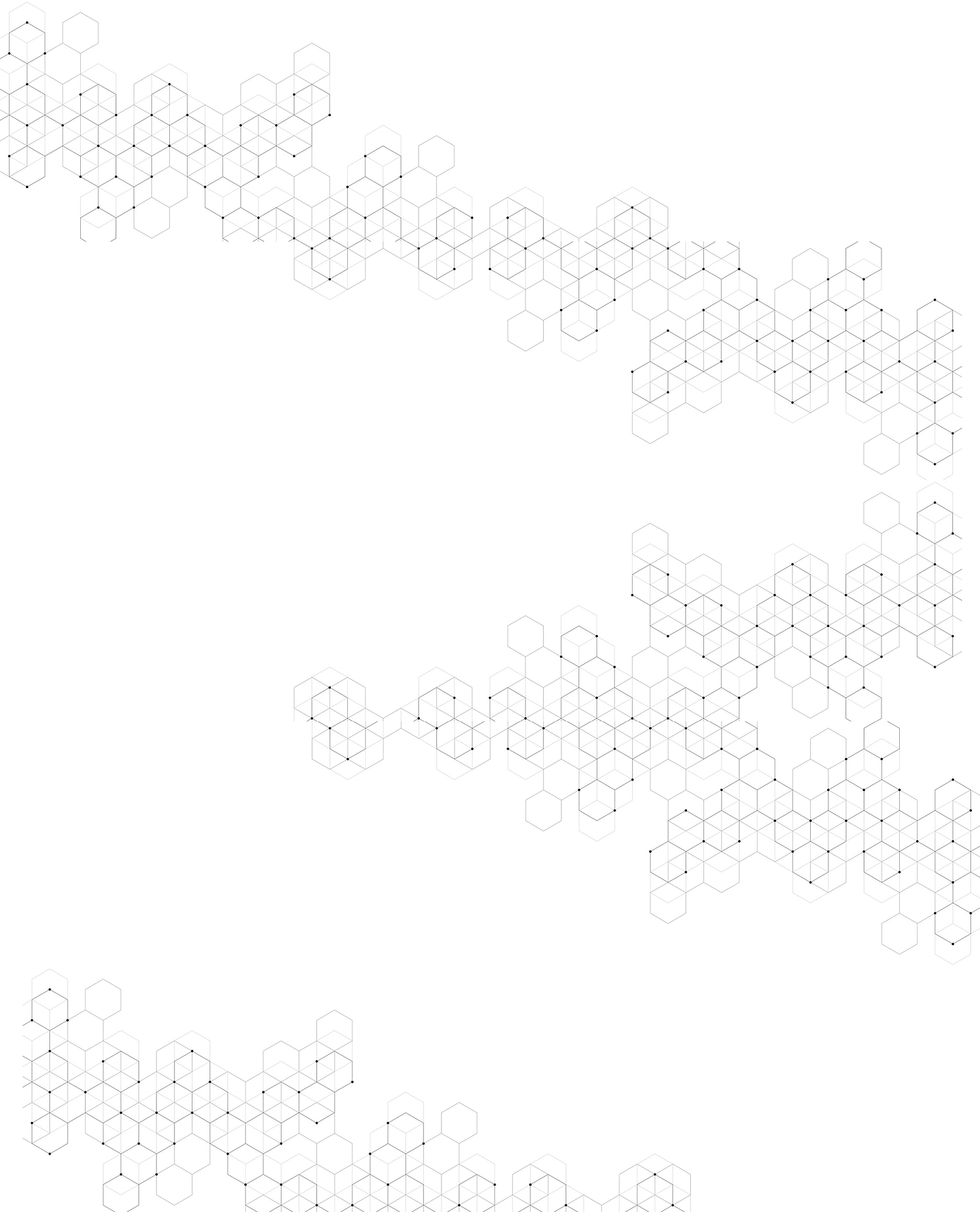

Measuring Pressure

This guide helps you with basic pressure concepts and with understanding how different pressure sensors work. There are a variety of sensors to choose from, each of which has its own operating principles, benefits, considerations, and drawbacks. After you decide on your sensor, you can consider the required hardware and software to condition, acquire, and visualize pressure measurements. You can also consider any hardware packages you may need.
What is Pressure
Pressure is defined as the force per unit area that a fluid exerts on its surroundings. The equation below demonstrates Pressure, (P), as a function of force, (F), and area, (A):
P = F/A
Pascal (N/m2) is the SI unit for pressure, but other common units include pounds per square inch (psi), atmospheres (atm), bars, and torr.
A container full of gas contains countless atoms and molecules that are constantly bouncing off its walls. The pressure is the average force of these atoms and molecules on the container's walls per unit of area. Moreover, pressure does not have to be measured along the wall of a container but rather can be measured as the force per unit area along any plane. Air pressure, for example, is a function of the weight of the air pressing down on Earth. Therefore, as the altitude increases, pressure decreases. Similarly, as scuba divers go deeper into the ocean, the pressure increases.
A pressure measurement can be described as either static or dynamic. The pressure in cases with no motion is static pressure. Examples of static pressure include the pressure of the air inside an oxygen tank or water inside a basin. Often, the motion of a fluid changes the force applied to its surroundings. Say the pressure of water in a kitchen faucet with the nozzle closed is 35 pounds per square inch (force per unit area). If one opens the nozzle, the pressure drops lower as the water exits the faucet. An accurate pressure measurement notes the circumstances under which it is made. Factors include flow, fluid compressibility of, and any external forces.
Measuring Pressure
A pressure measurement can be described by the type of measurement being performed. The three methods for measuring pressure are absolute, gauge, and differential. Absolute pressure is a reference to the pressure in a vacuum, whereas gauge and differential pressures are referenced to other pressures such as the ambient atmospheric pressure or pressure in an adjacent vessel.

Absolute Pressure
The absolute measurement method is relative to 0 Pa, the static pressure in a vacuum. The pressure being measured is acted upon by atmospheric pressure in addition to the pressure of interest. Therefore, absolute pressure measurement includes the effects of atmospheric pressure. This type of measurement is well-suited for atmospheric pressures such as those used in altimeters or vacuum pressures. Often, the abbreviations Paa (Pascal’s absolute) or psia (pounds per square inch absolute) are used to describe absolute pressure.

Gauge Pressure
Gauge pressure is a measurement relative to ambient atmospheric pressure. This requires that both the reference and the pressure of interest are acted upon by atmospheric pressures. Gauge pressure measurement excludes the effects of atmospheric pressure. These types of measurements include tire pressure and blood pressure measurements. The abbreviations Pag (Pascal’s gauge) or psig (pounds per square inch gauge) are used to describe gauge pressure.

Differential Pressure
Differential pressure is similar to gauge pressure, the difference is the reference of another pressure point in the system rather than the ambient atmospheric pressure. One can use this method to maintain relative pressure between two vessels such as a compressor tank and a line feeding the tank. Also, the abbreviations Pad (Pascal’s differential) or psid (pounds per square inch differential) are the applicable units.
The difference between measurement conditions, ranges, and materials used in the construction of a sensor lead to a variety of pressure sensor designs. One can often convert pressure to an intermediate form, such as displacement, by detecting the amount of deflection on a diaphragm positioned in line with the fluid. The sensor then converts this displacement into an electrical output in voltage or current. If the area of the diaphragm is known, one can then calculate pressure. Pressure sensors are packaged with a scale that provides a method to convert units.
Choosing the Right Pressure
The three most universal types of pressure transducers are the bridge (strain gage based), variable capacitance, and piezoelectric.
Bridge-Based Sensors
Bridge-based sensors operate by correlating a physical measurement, like pressure, to a change in resistance in one or more legs of a Wheatstone bridge. They are the most universal type of sensor because they meet a variety of accuracies, sizes, ruggedness constraints. Bridge-based sensors measure absolute, gauge, or differential pressure in both high and low pressure applications. They do this by using a strain gage to detect the deformity of a diaphragm subjected to the applied pressure.
When the diaphragm deflects due to a change in pressure, a corresponding change in resistance is induced on the strain gage, which you can measure with a conditioned DAQ system. You can bond foil strain gages to a diaphragm or to an element that is mechanically connected. If one uses silicon gages, they etch resistors on a silicon-based substrate and use transmission fluid to transmit the pressure from the diaphragm to the substrate.
Because of the simple construction and durability these sensors are ideal for higher channel systems. In general, foil strain gages are used in high-pressure (up to 700M Pa) applications. They also have a higher operating temperature than silicon strain gages (200 °C versus 100 °C, respectively), but silicon strain gages offer the benefit of larger overload capability. Because they are more sensitive, silicon strain gages are also often preferred in low-pressure applications (~2k Pa).

Capacitive Pressure and Piezoelectric Sensor
A variable capacitance pressure transducer measures the change in capacitance between a metal diaphragm and a fixed metal plate. The capacitance between two metal plates will change if the distance between these two plates changes due to applied pressure.
Piezoelectric sensors rely on the electrical properties of quartz crystals rather than a resistive bridge sensor. These crystals produce an electrical charge when they are strained. Electrodes actively transfer the charge from crystals to an amplifier built into the sensor. These sensors do not require an external excitation source, and are susceptible to vibration.

Capacitive and Piezoelectric Pressure Transducers are generally stable and linear, are sensitive to high temperatures, and respond quickly to pressure changes. For this reason, they are used to make rapid pressure measurements from events such as explosions. Because of their superior dynamic performance, piezoelectric sensors are the least cost-effective, and must be cared for to protect their sensitive crystal core.