Wind Tunnel Test Bench Improving Pro Cyclist Performance
- Feb 17, 2023
- 3 min read
Updated: Aug 28, 2023
*As Featured on NI.com
Original Authors: Mikel Fauri Larrea, Epsilon Euskadi SL
Edited by Cyth Systems

The compact size of the CompactDAQ and its versatility to acquire signals as diverse as those from load cells, various analog sensors, digital pulse input for speed, and analog outputs to set the resistance control set point, have made it possible to integrate the entire system in the minimum space possible."
- Mikel Fauri Larrea, Epsilon Euskadi SL
The Challenge
Develop a data acquisition system for the aerodynamics test of professional cyclists in a wind tunnel.
The Solution
Using NI CompactDAQ hardware and the LabVIEW software platform we created a versatile test operator system that provides real-time data logging, an intuitive user interface, and data visualization for the test operator (located in the wind tunnel’s exterior) and test subject (located in the wind tunnel’s interior).
Introduction
The competitive degree that professional cycling has reached today means that the difference between first and second place can be measured in a few seconds, within the framework of a three-week competition. That is why top-level cyclists cannot leave any detail to chance, and why they focus on those disciplines where the method and the study of controllable factors can bring some benefit, even if it is minimal, it can mean success. The individual time trial is the clearest example of this, and an improvement of a few grams in aerodynamic resistance can become a differential factor.
Requirements
As in any test carried out in a wind tunnel, the main objective is the measurement of the 6 components, forces, and moments, that act on the model, associated with the selected reference axis.
In this case, the model is the cyclist himself pedaling in conditions that are as close to the real world as possible. For this reason, it is necessary to introduce a system of rollers that simulates rolling resistance, adjustable in real-time according to the objectives of the test.
In the same way, it is necessary to measure the cyclist’s power output (in Watts) generated during pedaling, the cyclist’s speed on the rollers, the cyclist’s pedaling cadence, and other associated parameters. Other factors such as temperature, total and dynamic pressures, and relative humidity, are also measured. LabVIEW algorithms were used to determine aerodynamic coefficients and efficiencies to ensure optimal test conditions and the repeatability of the test.
The LabVIEW Real-Time data processing is paired with a set of cameras that gives video feedback to the cyclist under test about their performance and bike positioning.
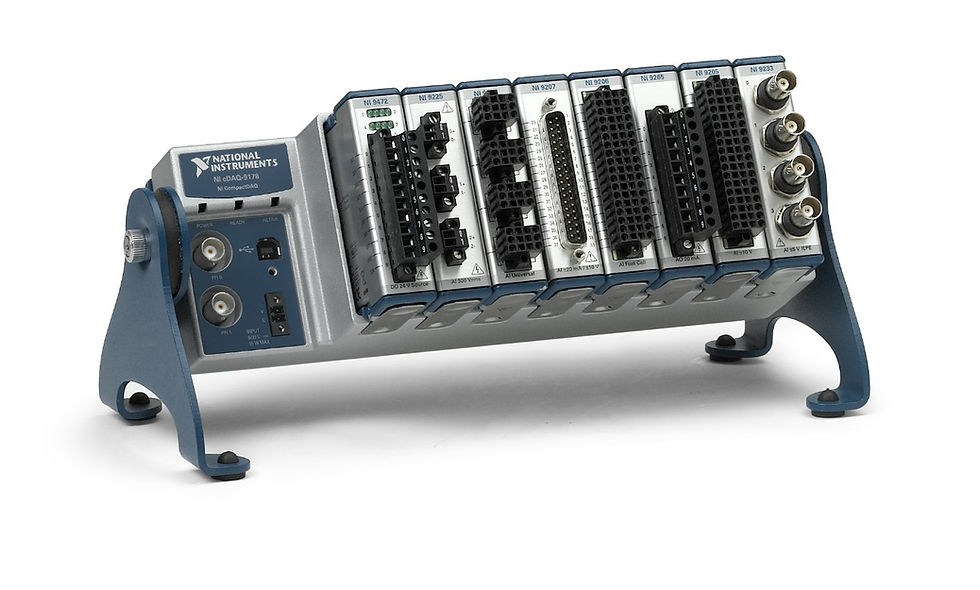
Summary of System Functions:
Data acquisition of forces and moments.
Acquisition of variable wind speed, dynamic pressure, temperature, humidity, and air flow.
Acquisition of rolling speed, rolling resistance, pedaling cadence, and power generated.
Calculation using LabVIEW algorithms and real-time processing of data and coefficients, and their storage for later analysis.
Video image capture and live playback for the operator and cyclist under test.
Test Bench
The test bench acquired all the data of the environment variables using sensor I/O incorporated into the wind tunnel. The force, torque, speed sensors, etc. for the cyclist and the bicycle, the electromagnetic hysteresis brake, and rotational servomotor, all were I/O acquired by the CompactDAQs.
Conclusion
The LabVIEW software architecture made it possible to in real-time acquire the data and develop software with an interface that allows it to be used simultaneously by the operator to control the test and by the cyclist himself to view his performance in real-time. Functions as diverse as the acquisition, processing, storage of data and the control of attached subsystems have been developed in very short periods of time, of the order of those contemplated in the main business area of Epsilon Euskadi: Motorsports of competition.
LabVIEW software architecture has made it possible to acquire data in real-time and display it in a synchronized format for the test operator and cyclist under test. Likewise, the compact size of the CompactDAQ has allowed us to acquire measurements from over 20+ sensors and integrate into the wind tunnel’s existing system with a minimal footprint envelope.
Author Information
Original Authors: Mikel Fauri Larrea, Epsilon Euskadi SL
Edited by Cyth Systems
Comments