Biotech Startup Accelerates Funding with Scalable Reference Design
- Dec 20, 2024
- 4 min read
Updated: Mar 30
Biotech startup secured millions in funding by demonstrating a bioreactor proof-of-concept in three months using Cyth’s embedded control system architecture.
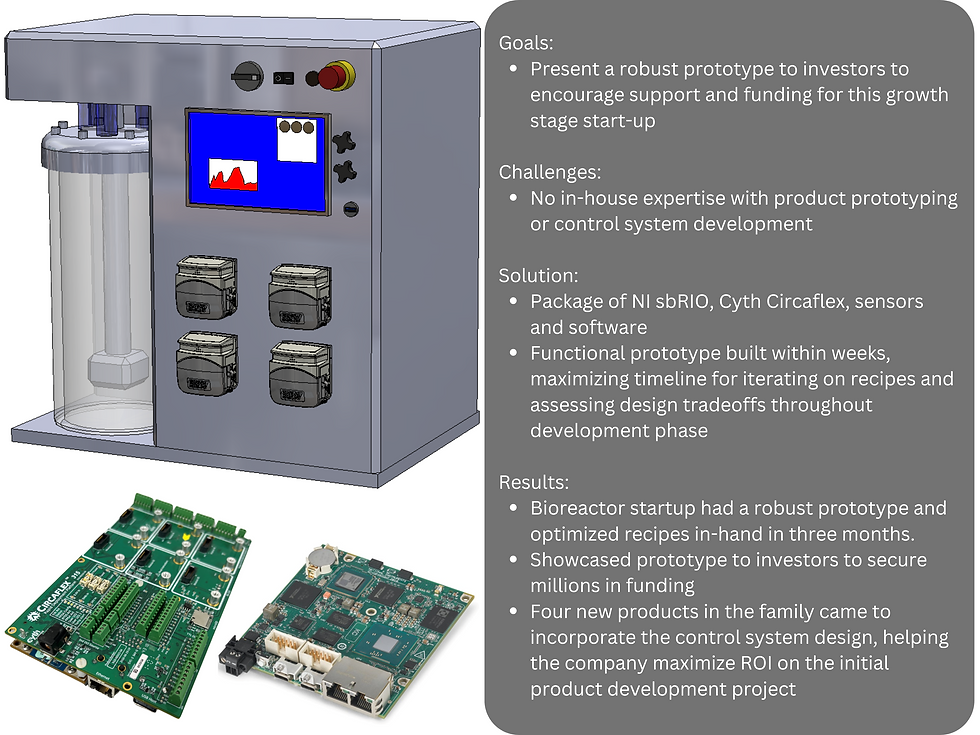
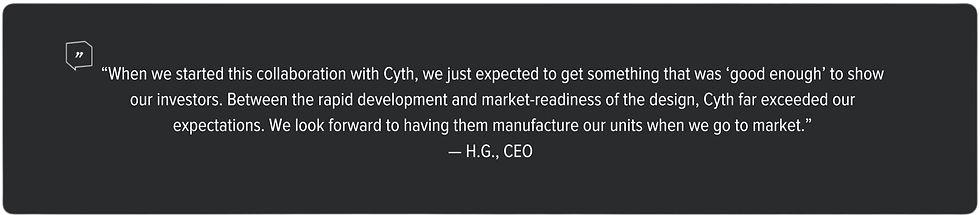
Curing the Uncurable
Many of us enjoy customizing simple things, like our order at a favorite café, but imagine personalization of the treatment of diseases like diabetes, or inoperable cancers.
Cell and gene therapies offer groundbreaking treatments for some of humanity’s most common and menacing diseases, yet their cost and production complexity hinder scalability. Cyth’s customer, a biopharmaceutical startup, developed a novel bioreactor technology capable of dramatically increasing the yield of cell-based therapies.
To secure investor confidence, they needed a flexible prototype to rapidly refine recipes with minimal downtime and waste. Time was critical, they required an optimized prototype and recipes within months to secure investor confidence and continue developing their innovative product.
By partnering with a control system design expert, they met their timeline, advancing their goal of making life-saving therapies accessible to more patients.
Flexibility or Performance? Why not Both?
Bioreactor systems are used for the research & development of biopharmaceuticals like vaccines, cell therapies, and gene therapies. The most expensive gene therapy available today costs $4.25M per dose (Buntz, 2024), with the average cost of gene therapies costing between $1M and $2M per dose (2023), making reliability and precise control during production a necessity.
These self-contained systems regulate all aspects of the cell culture vessel, including:
Temperature
Moisture
Carbon and oxygen levels
Mass flow valves
pH level
Depending on the cell-based therapy produced and intended yield volumes, there is a lot of variation in the number and type of system I/O, making it necessary to leverage a control system that is capable of coordinating complex control loops, while enabling flexibility in accommodating evolving production needs.
With plans to quickly raise a round of funding, then capture and expand market share by releasing a family of bioreactor models, this bioreactor startup recognized the importance of a flexible control solution that would enable them to quickly scale system I/O and build out their product line.

This startup had their product requirements finalized, but with a small team and minimal embedded design experience, they knew it would be challenging to develop a prototype on their own.
Starting Closer to the Finish Line
To get their products to market quickly while optimizing reliability, this startup decided to work with a product design expert.
For the job, they turned to Cyth Systems because of their proven success in designing novel Life Sciences equipment for broad-based customer adoption.
Cyth worked with this company to transform their requirements into a design, including a core control system, sensors, mechanicals, and a project plan for rapid design iteration, including:
Creating a prototype system within weeks
Incorporating the company’s ongoing product feedback from firsthand use over the course of weeks
Refining the design into a robust product that is easily manufactured

This startup’s proof-of-concept system required integration of:
Stepper drives (x4)
pH module
Carbon, oxygen, and nitrogen level sensor module
Temperature module
Mass flow (gas release valve) control module
Fluid flow control module
Cyth selected the NI single-board RIO (sbRIO) platform for its:
Deterministic control and processing capabilities
FPGA-enabled coordination of complex control loops
Native compatibility with LabVIEW and LabVIEW FPGA software, enabling the rapid implementation and modification of control and processing features

The CircaFlex platform enhanced the sbRIO’s capabilities by:
Simplifying connectivity and signal conditioning to mitigate the need for custom hardware development
Enabling rapid I/O module integration
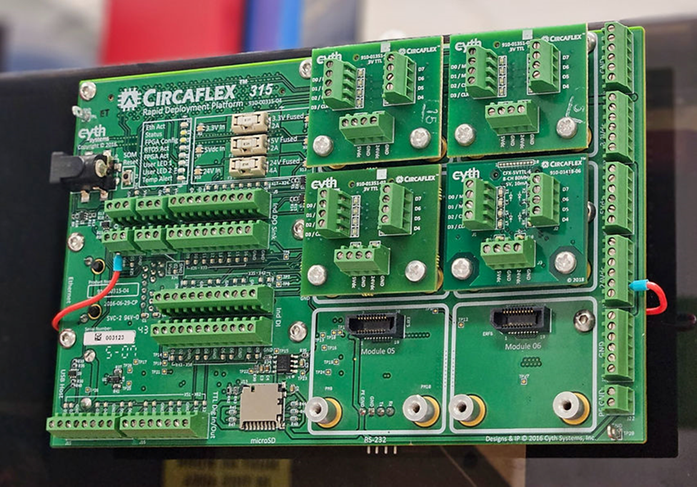
The sbRIO and CircaFlex hardware, paired with Cyth’s field-tested bioprocess software architecture, allowed for rapid implementation and refinement of the startup’s control loops. The prototype enabled them to test out their bioprocesses and assess the machine’s usability.

Through this approach of rapid prototyping and iteration, this startup had a Cyth-tested prototype within a matter of weeks that included:
High-quality measurements
Tight synchronization between complex control loops
Simple UI to enhance and facilitate user experience
Flexibility to modify recipes in real time
The flexibility of Cyth’s bioprocess control reference architecture enabled this startup to reuse the design for multiple products, helping them rapidly expand their offerings with a solution that scales from R&D through full-scale pharmaceutical manufacturing.
The major components included in the final design were:
Cyth CircaFlex-315
NI LabVIEW
NI LabVIEW FPGA
Accelerated Time to Funding
The rapid development cycle and rigorous parallel testing enabled this startup to demonstrate the prototype to investors in three months and exceed their initial funding goals.

For investors, the most compelling elements of this bioreactor startup’s prototype were:
Unprecedented cell growth yields, poised to disrupt the bioreactor industry
Market-readiness of prototype with a low-risk and high-ROI R&D investment
Reliability of system, built on an industry-standard hardware platform with a field-tested software architecture
The solution was designed with scalability and repeatability of recipes in mind. The robust, intuitive user experience mitigates the learning curve for users and encourages adoption from the lab through commercialization. System uptime reduces the risk of wasted reagents, and precise control paired with continuous monitoring ensures the execution of recipes exactly as specified by the operator.
As this startup prepared to go to market, they wanted to expand their product line to include more sizes and variants of bioreactors. The flexibility of the embedded reference design made it quick and easy to scale up production on all product lines simultaneously.

Citations
Buntz, B. (2024, April 26). With costs up to $4.5M, cell and gene therapies redefine norms. Drug Discovery and Development. https://www.drugdiscoverytrends.com/how-price-safety-and-efficacy-shape-the-cell-and-gene-therapy-landscape/
Staff, G. (2023, December 27). Cell and gene therapy manufacturing costs limiting access. https://www.genengnews.com/insights/cell-and-gene-therapy-manufacturing-costs-limiting-access/
We offer a 30% discount on first bookings of Russian Delhi Escorts on Client Request.